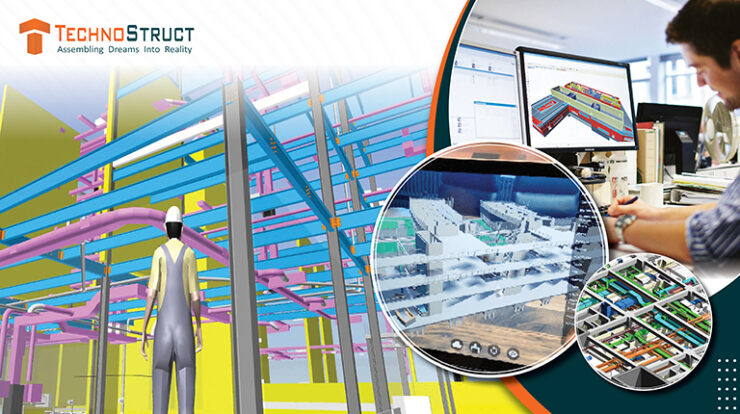
In buildings, the Mechanical, Electrical, and Plumbing (MEP) system provides services to people’s daily Requirements and hence plays an important role in creating a comfortable and safe environment for building Users.
MEP Engineering Includes Execution and management of Non -Structural Components Like HVAC (Heating, Ventilation, and Air cooling), Plumbing(Domestic and Fire), Mechanical equipment, and Electrical components.
Phases in Lifecycle of a construction Project –
- Planning.
- Design and analysis
- Development
- Execution
- Operation and Maintenance (O&M)
The O&M phase takes most of the time, resulting in the highest cost among various phases within the lifecycle of a building.
In fact, previous studies indicated that, the cost associated with the O&M could take up to 60% of the total project cost
Along with that Research shows That Maximum Wastage occurs in O&M stage.
Thus To optimize O&M management, improving the efficiency of the MEP system is critical .
In Traditional scenarios, Required information about specific equipment can only be found manually from the bulk of the project completion documents (in the form of electronic or hardcopy documents).
In This Case low efficiency of manual search may lead to waste of Valuable Resources i.e Time and Labour.
This is Because much of the information used is is still paper-based and is delivered to the owner months after the facilities are in use.
Therefore, in order to optimize resources, it is necessary to understand Building Information Modeling (BIM) and its related use within buildings during the operations and maintenance phases.
BIM-Building Information modelling-
BIM is a process of creating and managing information of a construction project throughout its lifecycle. As part of this process, a coordinated digital description of every aspect of the Asset is developed, using an appropriate set of technologies. This digital description is likely to include a combination of information-rich 3D models and linked structured data, such as product, Site-execution, and delivery information.
Use Of BIM can Give Insights to Facilities Management Team in Form of Data (Information) which can lead to Efficiency in Operation and Maintenance of Building.
This Data Can be Captured During the Preconstruction and Commissioning Stages.
For Eg if A Pumping equipment is to be installed Information Ralated to Maintainace such as
- Discharge of Pump.
- Make And Details of Manufacturer of Pump
- Electrical Rating.
- AMC contract For maintenance of Pump if any .
Every relative information Should Be Captured and integrated with BIM Model.
In some cases, field project execution teams are often forced to make immediate decisions due to unforeseen field conditions. These design changes, no matter how small, must be captured throughout the construction phase and integrated into the BIM model.
Adopting an integrated BIM project delivery approach ensures that the same BIM models created during the design phase are incorporated with additional information during construction planning, coordination and fabrication.
Information from the design phase through construction to final commissioning of the building is captured and continuously integrated into his BIM models. This can be used to represent the as-built dataset model of the building.
This as-built BIM model can be used for operations, maintenance, and future retrofit purposes
Benefits-
Proactive Maintainance-
Maintenance of MEP components can be performed using built-in information embedded in as-built BIM models.
Facility managers can proactively schedule maintenance, repair, and replacement work based on model Information i.e name,warranty, maintenance manuals, and maintenance logs for all components..
Retrofitting-
These As-Build Models Can serve As Reference Files For Future Retrofitting Activities.
Facility managers are better informed about the existing condition of the building, allowing them to make renovation decisions with minimal complexity while minimizing cost impact.
Energy-
The integrated information embedded in the BIM model helps facility managers and owners analyze and compare various energy alternatives thereby enabling them to adopt the most environment-friendly and economic approach
Continuous tracking of the various building performance factors such as daylighting, comfort, water consumption, low to zero carbon technologies and materials’ environmental impact enable them to formulate the best energy consumption strategy with minimum operational costs.
Improved Collaboration-
BIM enables Seamless Exchange of Information between key people involved in design and Construction.
Facilities manager can get involved in design phase Creating an Opportunity to Address design and Construction Constraints .
Which can ensure that the facility is Economical and in alignment to the day-to-day objectives of facility management Activity.
BIM Co-ordination-
BIM Co-ordination is a Process of Determining Inter disciplinary Clashes At early stage So that Clashes would be Rectified and clash free Data(i.e Shop Drawings ) can Be used For execution.
If uncoordinated Data is utilised for execution it Tends To create chaos at the time of Operation and maintenance As it directly affects the Quality of work and Desired output.
Stratagic and Real time Maintainance –
Once an As-built Model is Ready it opens avenues for faster, better, and technology enebled O&M activities By promoting use of tools Like YouBIM which is an intuitive platform to have all the facility’s information centralized, digitalized, and accessed from anywhere.
Users can quickly find any piece of equipment, room, or system and retrieve the relevant information with just a few clicks.
Use of such Tools Again simplifies overall process of O&M.
Thus the use of Digital Model i.e BIM model can Directly optimize overall process of Operation and maintainance