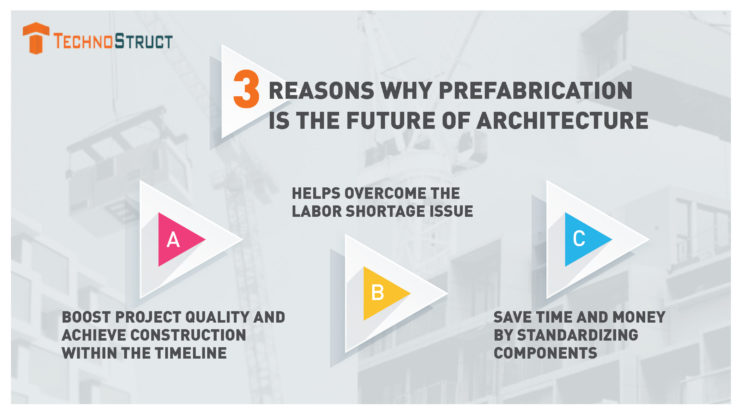
The construction sector is one of the fastest-growing sectors on account of the ever-evolving living requirements that come with urbanization and the need to design and build best-in-class and high-value structures for various purposes – residential, offices, entertainment, and whatnot. Today, the construction industry employs about 7 percent of the world’s working-age population and is one of the world economy’s largest sectors, with $10 trillion spent on construction-related goods and services every year, as per a new McKinsey Global Institute report.
The introduction of prefabrication technology in the construction industry has helped answer and solve several construction challenges, but the technology has not captured the market at a similar pace. Even though according to a survey conducted by McGraw Hill, 66% of the respondents (contractors) claimed that prefabrication and modularization help shorted project timelines by 4 weeks or, in some cases, by half. Further, contractors believe that prefabrication and modular construction have the capability to improve productivity by 92%, help establish a competitive advantage by 85%, and generate greater ROI by 70%. The study also suggested that BIM’s application allowed 77% of the contractors to use prefabrication on larger, more complex projects.
Fact: The iconic 21-story, 500-room hotel, San Antonio’s iconic Hilton Palacio del Rio, opened in 1968. It was one of many architectural attractions designed for the 1968 World’s Fair, which was designed and built in only 202 days, a timeline made possible by the extensive use of modular construction techniques. Every room was built and furnished in its entirety in an off-site facility and subsequently installed by a 300-ton super-crane, a practice that helped the developers condense onsite construction into a 46-day window.
Today, a couple of buildings originate with the core idea of prefab technology, but the case was not the same a couple of years ago. Here are 3 reasons why it is the future of construction today and why they will influence the AEC industry in the coming years:
Boost Project Quality and Achieve Construction within Timeline: Prefabricated construction is done within a controlled environment specifically designed to manufacture and assemble individual prefabricated components. This allows the designer, contractor, and engineers to run quality checks and review the complete process, which would not have been possible in traditional construction methods. The project site is safe, organized, and clutter-free, which improves productivity and reduces any accidental risks. Prefab also offers optimized workflow and process – as the same team builds and assembles the structure in a controlled environment.
Fact: Pipa House by Bernardes Arquitetura, Porto Feliz, SP, Brazil, winner of the 2019 Popular Choice A+Award in the Architecture +Prefab category. The prefabricated concrete house was designed for building efficiency “through an industrialized system that allowed its rapid execution and very low waste production.
Helps overcome the labor shortage issue: The prefabrication construction method employs less labour than traditional methods and frees up time for field workers to cover more prefab projects – and help mitigate the problem of the skilled labour shortage.
Fact: Clinton Corners by Lake|Flato Architects, Clinton Corners, NY, winner of the 2019 Jury A+Award in the Architecture +Prefab category. Fabricated in a nearby facility, the exposed heavy timber frame and super-insulated wall panels were delivered to the site and assembled in less than three weeks.
Save time and money by standardizing components: The integration of building information modeling with prefabrication saves a lot of time in overcoming measurement miscalculation issues. Further, pairing prefab construction with VDC is an intelligent process that limits project variability and allows one to better manage schedule and budgets.
Conclusion:
In this changing climate, prefabrication is the perfect tool to build a house, commercial complex, or an entertainment hub with a high degree of customization, competitive pricing, quick turnaround time, and fewer resources. BIM-driven prefabrication has just been able to scratch only the surface and has a lot in store for the future.
TechnoStruct LLP is a leading BIM Service Provider in C.A. that specializes in providing mechanical and engineering solutions, designing, solar engineering solutions, and construction solutions to commercial projects across industries, with a diversified range of services including but not limited to BIM consulting services, Mechanical Electrical Plumbing (MEP) engineering and designs, Mechanical Subcontractor, Solar, Electrical Subcontractor, and many more.