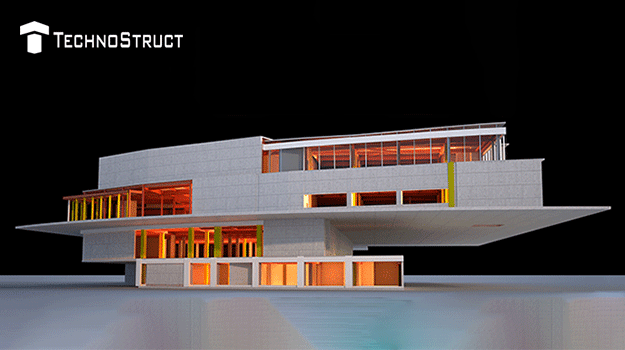
The Past: We all understand how traditional construction surveys are conducted out by securing a fixed point of reference, a baseline and a network of vertical and horizontal checkpoints, through which spatial data can be captured. Historically, this has been achieved by using measuring chains and theodolites – a combination still used today.
The Future : The latest technology to capture building spatial data in the construction industry has the capability to digitally capture a physical space or site, from the ground or from the air, using the information to create an ‘intelligent 3D model’ which is often progressively referred to as ‘Scan-to-BIM’.
Why should you invest in BIM compatible technologies?
The construction market manages to operate at low margins, so greater accuracy and transparency at an initial stage encourages contractors to diminish their risks and therefore put forward more realistic bids.
For example, a detailed BIM model can help them accurately calculate material volumes and areas, and plan how much material they can stock on site and the human hours needed to get the job done. Of course, getting 3D scanning and modeling work done up front arises at a cost, especially compared to traditional 2D surveys, since it can result in principal savings. The case for Scan-to-BIM becomes even more compelling when you consider the potential savings in the long haul, that transparent data sharing and prompt engagement in intelligent 3D design can bring to your projects.
Surveying Technology is advancing as we speak, or read. Theodolites are being outdated by Surveying stations. The main inference of total stations is that they blend the functionality of theodolites with electronic distance meters, allowing them to precisely capture data for BIM or CAD software.
Recently the industry witnessed another breakthrough in the technological shift, with the total stations enhanced & even completely substituted by an efficient and proactive Laser Survey method and Drone capture, which has dramatically reformed and revolutionized a new age in BIM processes.
BIM Technology is currently facing certain limitations while adapting to ever-changing technology. Stern Scheduling would be one such reason.
Constructions teams can overcome this challenge. They can do this by accumulating and processing image data on a regular, timely basis to avoid the aforementioned. A single tripod-mounted laser scanner can amazingly measure the precise distance of a million spatial points per second, creating a “point cloud” that can be expended to generate complex 3D models. This eradicates the need and the cumbersome workload to measure individual points resulting in substantial time savings. This technology has seized the industry’s imagination, with its promise of turnkey “scan-to-BIM” functionality.
Surveying companies are often able to deploy a combination of three principal technologies to seize the 3D data. The quintessential terrestrial tripod-based laser scanners are able to record interior spaces and exterior porticos, or tough to reach mechanical and electrical installations or plumbing, concealed in walls or behind ceiling tiles with reliable ease.
In the same realm of functionality, Drones have become an increasingly resourceful tool. In particular, they are allowing construction firms to lower costs, speed up their processes and increase site safety. This is where using drones for BIM thrusts into action.
There are a number of key areas in which Drones can make the BIM process easier. This includes:
- Conducting structural inspections without the need for human labour
- The aptitude to carry out site inspections prior to construction start
- Using progressive point cloud scanning
- Taking aerial photographs throughout the build progression
- Keeping a close eye on-site activity to ensure safety and progression is continued
- Project Completion inspections
- Meeting government regulations
Synergizing Drones with the BIM process leads to infinite possibilities! High-end drones can now emit visual feeds in stunning HD quality letting you access high-quality footage of how the construction site would look from anywhere in the world.
In addition to terrestrial and mobile scanners, high-resolution photos acquired by drones fitted with top drawer cameras can be synergized using software running complex algorithms via a process called Photogrammetry.
Photogrammetry is the science of taking measurements from photographs. Fundamentally, it allows construction crews to take digital photos of a site or building, upload it onto a computer, and generate a cohesive 3D model. It can be more versatile and can be used in tight indoor spaces. At the same time, aerial site data can also be easily captured via drones. While photogrammetry typically cannot generate the millimeter level dense detail of a laser survey, it can produce highly accurate details and is comparatively more cost-effective.